In the field of modern electronic manufacturing, PCBA (Printed Circuit Board Assembly) is the core component of electronic products, and its processing quality directly determines the performance, reliability, and service life of the product. From raw material storage to finished product delivery, PCBA processing involves numerous complex processes, and any negligence in any link may lead to quality issues. Therefore, it is crucial to establish a scientific and systematic quality control system. To ensure high yields and reliable electronics, manufacturers must enforce strict quality control (QC) at critical stages (Top 8 SMT Quality Control Key Points You Can’t Ignore For PCBA Production).
Here are the Top 8 SMT Quality Control Key Points You Can’t Ignore For PCBA Production that can make or break your PCBA production:
1. First Article Inspection (FAI) – The Critical Starting Point

FAI Inspection
Why it matters: Validates that the initial production run meets all design specifications before full-scale manufacturing begins.
Key checks:
A. Full design verification (compare actual PCBA against CAD data)
B. Process validation (confirms manufacturing parameters are correct)
C. Documentation review (BOM, assembly drawings, and work instructions)
D. Comprehensive testing (electrical, functional, and dimensional checks)
2. Solder Paste Inspection (SPI)
Why it matters: Improper solder paste application (volume, alignment, or stencil issues) causes defects like bridging, insufficient solder, or tombstoning.
Key checks:
A. Paste thickness & coverage (via 3D SPI systems)
B. Alignment with PCB pads
C. No smearing or bleeding
3. Component Placement Accuracy
Why it matters: Misaligned or missing components lead to electrical failures.
Key checks:
A. Pick-and-place machine calibration
B. Verification via Automated Optical Inspection (AOI)
C. Correct polarity & orientation of ICs, diodes, etc.
4. Reflow Soldering Profile Validation
Why it matters: Incorrect temperature profiles cause cold joints, voids, or thermal damage.
Key checks:
A. Preheat, soak, reflow, and cooling rates (per solder paste specs)
B. Thermocouple-verified oven profiling
C. No overheating of sensitive components
5. Automated Optical Inspection (AOI)
Why it matters: Catches defects early—before costly rework.
Key checks:
A. Solder joint quality (shiny, concave fillets)
B. Component presence, alignment, and polarity
C. No solder bridges or lifted leads
6. X-Ray Inspection (for BGA & Hidden Joints)
Why it matters: Reveals hidden defects in Ball Grid Arrays (BGAs) and QFNs.
Key checks:
A. Voiding percentage (<25% typically acceptable)
B. Ball alignment and collapse uniformity
C. No cracks or cold joints
7. In-Circuit Testing (ICT) & Functional Testing
Why it matters: Ensures electrical functionality and detects manufacturing flaws.
Key checks:
A. Continuity, shorts, and opens
B. Power-up functionality (if applicable)
C. Firmware/software validation
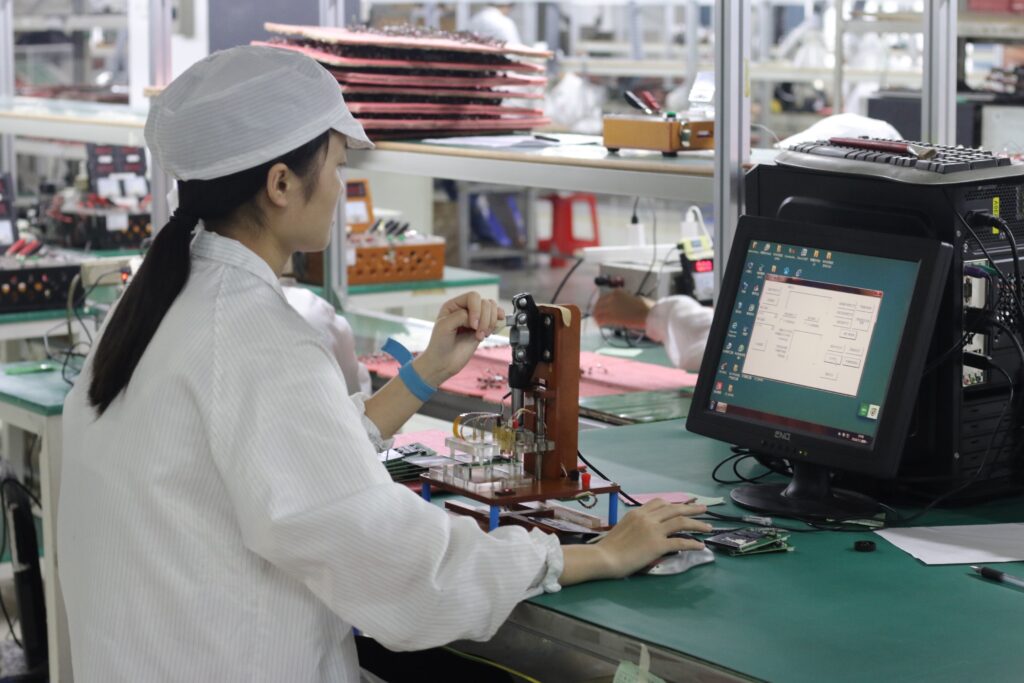
8. Final Visual & Manual Inspection
Why it matters: Human eyes catch subtle defects machines might miss.
Key checks:
A. Mechanical damage (scratches, bent pins)
B. Cleanliness (no flux residue or debris)
C. Connector alignment and labeling
Conclusion
Skipping any of these SMT quality control checkpoints risks defective boards, field failures, and recalls. By implementing FAI, SPI, AOI, X-ray, and functional testing, manufacturers can achieve:
- >99% first-pass yield
- Lower production costs
- More reliable end products
Pro Tip: Combine automated inspection with periodic manual audits for maximum defect detection.